Stonebloc Expands Product Offering with Innovative Wedge and Stair
When we launched Stonebloc in 2015, it was in response to the demand for a longer lasting, better looking, and faster to install residential retaining wall product. Since then we’ve remained committed to innovation, and . We're proud to announce the launch of two new products; the Stonebloc Wedge Block and the Stonebloc Stair Block.
These new products round out the range allowing curves to be built into Stonebloc walls, and more importantly eliminating the need for boxing and pouring steps instiu on site.
Stonebloc Wedge Block
Creating curved walls is simple with Stonebloc's Wedge Block. Available in left and right, and standard and flat top variations, this block offers the same benefits as seen across the whole Stonebloc range:
- Easy installation: Two labourers can build up to 120m2 of wall per day. The self-aligning and interlocking elements of these modular concrete blocks make it quick to create retaining walls.
- Vertical walls on the boundary: Stonebloc walls are built vertically on the boundary with no incline, maximising land availability.
- Designed for Deconstruction: Stonebloc is a modular concrete block building solution. This means it's just as easy to deconstruct a wall for maintenance as it is to build it.
- Timeless Aesthetic: The split stone facia is designed to work across many different designs with a timeless finish.
- Durable concrete: Made from a minimum 20MPa concrete, you can trust these interlocking blocks are designed to withstand the elements.
- Sustainability: By using our Total Precast Solution offering, you can choose one of three concrete mixes and control the reduction in embodied carbon.
Stonebloc Stair
Like the Stonebloc Wedge Blocks, the Stair Blocks also offer the same benefits as the rest of the range. Two benefits that are specific to the Stair Blocks are:
Benefits of the Stonebloc Stair include:
- Complement Stonebloc retaining walls: Often there are challenges associated with traditional methods of construction stairs alongside retaining walls, which often involve costly and time-consuming processes like concrete pouring or the use of less durable timber. Stonebloc Stair Blocks have been designed to complement the whole retaining wall, extending the split stone facia throughout the design.
- Code-compliant rise and tread dimensions: These blocks are designed to meet all relevant building codes.
Bespoke Stonebloc Retaining Wall Designs
With the addition of the Stonebloc Wedge Block and the Stonebloc Stair, Stonebloc you now have the ability to create more bespoke Stonebloc retaining wall designs.
To start using the Wedge and Stair Blocks in your Stonebloc designs, reach out to us today
When it comes to building retaining walls, sea walls, or other large-scale structures, concrete blocks are often the go-to solution due to their durability and strength. However, choosing between large modular concrete blocks or small modular concrete blocks can be tricky. Large blocks may be more efficient for quickly constructing a large wall, while small blocks can offer more flexibility and customization options. In this blog, we will compare both and explore the benefits and drawbacks to help you make an informed decision for your next project.
What are modular concrete blocks?
Modular blocks (also known as interlocking blocks), are precast concrete elements that are designed to fit together seamlessly. They come in a variety of sizes and shapes and can be used in a wide range of construction projects.
With modular construction, comes design flexibility. No matter what you’ve chosen, you can often use large or small blocks for retaining walls, seawalls and erosion protection. Their interlocking design allows them to be stacked on top of each other without the need for mortar or other adhesives, making them quick and easy to install. Made from concrete, blocks are durable, weather-resistant, and require minimal maintenance. This makes them a popular choice for a variety of commercial and residential applications.
Large and Small Modular Block Retaining Walls
Large modular concrete blocks have to be installed with machinery as they’re too heavy/big to place by hand. Depending on what range you choose, blocks can weigh from 150 kgs to over 1500 kgs (1.5 tonnes). Because of their size and weight, they are often used instead of traditional options like tilt slab or timber, as they can be assembled quickly and with less labor inputs. The Interbloc and Stonebloc systems have large modular concrete blocks as the primary element in their ranges.
Interbloc Installation
Stonebloc Installation
In many instances, small modular blocks can be installed by hand. Ranging from around 100-300mm wide and weighing from 8-30 kgs, heavy machinery is not often needed for installation. Like their large block counterparts, you can use these blocks for larger structures such as tall (above 2m) retaining walls and seawalls. They are more catered to smaller projects, however. Commonly used in landscaping projects, garden walls, and other smaller scale structures. Despite their smaller size, small modular concrete blocks are still durable and long-lasting, making them a practical choice for a variety of residential and commercial projects.
Features of Large and Small Modular Blocks
- Size and Weight: Large modular concrete blocks are significantly larger and heavier than standard concrete blocks, making them capable of withstanding high amounts of pressure and weight. Small modular blocks can still achieve much of the outcomes that larger blocks can, they may just need more components to do so
- Interlocking Design: Much like LEGO, these blocks have an interlocking design that allows them to be stacked and locked together. This feature makes them quick and easy to install, saving time and labour costs. In the case of Interbloc and Stonebloc, the combination of their size, weight, and interlocking shear key allows overturning forces to be resisted
- Durability: Concrete is designed to withstand harsh weather conditions, erosion, and other environmental factors, making them long-lasting and low-maintenance. For Interbloc and Stonebloc, there is a minimum 20 MPA.
- Versatility: These blocks can be used for a wide range of applications for various industries including construction, civil, rural, and more.
- Cost-Effective: Overtime, the cost of large modular blocks can be more efficient compared to traditional systems. With lower maintenance requirements and non-destructive dismantling you can build for now and plan for the future.
With these blocks, try building:
Application | Large Modular Concrete Blocks | Small Modular Concrete Blocks | Image Example | |
Gravity retaining walls | ✅ | ✅ | ![]() | |
MSE retaining walls | ✅ | ✅ | ![]() | |
Seawalls | ✅ | ![]() | ||
Aggregate Bins | ✅ | ![]() | ||
PKE/Feed Bins | ✅ | ![]() | ||
Fertilizer Bins | ✅ | ![]() | ||
Culverts | ✅ | ![]() | ||
Silage Bunkers | ✅ | ![]() | ||
| ✅ | ![]() | ||
| ✅ | ![]() |
Pros and cons of Large and Small Modular Blocks
LARGE MODULAR BLOCKS
Speed of installation is one of the largest benefits you’ll gain with a large modular concrete block. With our own ranges - Interbloc and Stonebloc - two people can build from 120-160m2 of wall per day. Adding to the installation efficiency, you don’t need to add mortar or other adhesives. Being made of strong concrete (for our blocks, it’s a minimum of 20 MPA), large modular concrete blocks are resistant to harsh weather conditions, erosion, and other environmental factors . With worsening weather throughout New Zealand, this will reassure you that your structures will be long-lasting.
Typically, large modular concrete blocks have low maintenance requirements making them a practical and sustainable option. Interbloc is more sustainable than the standard large blocks. Made for high-quality certified wet excess concrete, they’re low carbon, zero waste (verified by an EPD). Overall, the combination of these advantages makes large modular concrete blocks an attractive option for construction projects that require a durable, efficient, and cost-effective solution.
Access and design flexibility are the two main areas where large modular concrete blocks perform weakly. With blocks being around 1m long and up, equipment large enough to lift the blocks is needed. Getting this machinery on-site requires space for loading/unloading, ruling out tight sites (and therefore large modular blocks).
For larger concrete blocks like Stonebloc, heavy machinery like an excavator is needed for installation.
Depending on the range that you choose, large modular concrete blocks may not be able to accommodate complex curves or angles. This will result in changes to a design or custom blocks to fit the project - both which Interbloc and Stonebloc can assist you with.
SMALL MODULAR BLOCKS
Maneuverability and flexibility are the biggest advantages to small modular concrete blocks. Although you can build large developments with this, small projects can be more difficult to use. Additionally, small modular concrete blocks are highly versatile and customizable, coming in a variety of sizes, shapes, and colors, allowing for creative design options. Another advantage of small modular concrete blocks is their durability. They are made of high-quality concrete materials that can withstand harsh weather conditions, erosion, and other environmental factors, making them a long-lasting option for construction projects. Finally, small modular concrete blocks are cost-effective, as they require less labor than traditional masonry construction methods, resulting in cost savings for construction projects. Overall, the combination of these advantages makes small modular concrete blocks a practical and efficient option for construction projects that require a durable, cost-effective, and customizable solution.
To achieve great heights and lengths of retaining walls, small modular blocks can be inefficient. With smaller facial m2, installation for larger projects can be labored. Coupling this with some smaller block solutions needing fiberglass pins per block for vertical reinforcing, you may have an installation with a long duration (costing you time and money).
Comparison of Large and Small modular concrete block retaining walls
Both large and small modular block options have their advantages and disadvantages. However, large modular concrete blocks offer several distinct advantages that make them a superior option for many construction projects.
One of the main advantages of large modular concrete blocks is their size and weight. While this can be seen as a potential disadvantage, their size and weight also make them highly durable and able to withstand harsh weather conditions and environmental factors. Large modular concrete blocks are ideal for large-scale projects that require significant structural support, such as retaining walls, sea walls, bins, and bunkers.
In addition to their durability, large modular concrete blocks also offer an efficient and cost-effective solution for construction projects. Their easy and quick installation process, requiring less labour than traditional poured concrete construction, makes them a practical option for projects with tight timelines and budgets. Additionally, their interlocking design eliminates the need for mortar or other adhesives, resulting in a faster and more efficient assembly process.
Large modular concrete blocks are also highly versatile, coming in a variety of sizes, shapes, and colors. This allows for creative design options and customization for specific project requirements. Finally, large modular concrete blocks are a low-maintenance option, requiring minimal upkeep and providing a long-lasting solution for construction projects.
While small modular concrete blocks may have some advantages, such as ease of installation and high customizability, they may not be suitable for larger-scale projects that require significant structural support. Additionally, their interlocking design may limit the complexity of design options available.
In conclusion, large modular concrete blocks offer several advantages that make them a practical and efficient option for many construction projects. Their durability, easy installation process, versatility, and low maintenance requirements make them a superior option over small modular concrete blocks for large-scale projects that require significant structural support.
Government has a clear goal of increasing housing density within urban areas. Higher density housing often requires extensive retaining to flatten land and make the construction of houses easier. There is also an increasing focus on the environmental effects of how we build, and the sustainability of the materials we use.
Why are retaining walls needed?
Retaining walls are used to hold back a bank of earth when there is a change of level. There are many types of retaining walls including gravity, cantilever, and mechanically stabilised earth (MSE) (Build Magazine).
Common examples of using a retaining wall include:
- When there is a sudden & steep change of gradient in the level of the land
- Multi-tierred or terraced garden
- There is erosion
- Needing better water drainage
Stonebloc is primarily a gravity- based retaining wall system. This type of retaining wall relies on the combined weight of concrete blocks to resist overturning forces. Simply, gravity retaining walls work by using their own weight and the weight of the soil they are holding back to provide stability.
Subdividing and maximising land with Stonebloc
Land subdivision is the process of dividing a piece of land into smaller sections or lots. These lots can then be sold, developed, or used for different purposes. Typically thought of as a residential process, subdividing land also benefits the wider community. Usually, this is done by creating public spaces and infrastructure. All land subdivisions must meet council requirements to meet safety and sustainability standards.
Stonebloc retaining walls offer a versatile solution for land subdivision. When subdividing with Stonebloc, you’ll benefit from:
- Generic Designs: Off-the-shelf retaining walls designs ranging from 5kPa to 12kPa and up to 2 meters high which meet building consents
- Maximised Land: Build retaining walls right up to the boundary line
- Fast Installation: 2 labour units can build up to 120m2 per day, allowing your subdivision to finish faster
For more specific designs, we can provide contacts for independent engineers experienced in designing with Stonebloc. By using Stonebloc for subdivision, property owners can divide their land in a way that meets council requirements while maximizing space. The modularity of Stonebloc makes it an ideal option for both greenfield developments and existing properties. With Stonebloc, land subdivision can be done efficiently and cost-effectively, while still meeting all necessary requirements for safety and sustainability.
Maximising the lifespan of your wall
Retaining wall structures is a long term structure. In New Zealand, the minimum design life of a retaining wall is 50 years, but in practice the wall will be around much longer then that. Retaining walls build using durable materials offer long term sustainability benefits, as the saying goes ‘build it once, build it right’.
Unlike traditional options (i.e timber retaining walls), Stonebloc doesn’t decay over time. This means that they are a low-maintenance and long-lasting option.
In contrast with other building systems, Stonebloc can be non-destructively dismantled during the life of the wall for easier maintenance, and at the end of life of the wall. The blocks can be reused. There is no effect on the structural integrity of the wall. This is almost unique to Stonebloc.
Divide your land and reduce environmental impact with Stonebloc
Stonebloc retaining walls divide land and reduce environmental impact. They are made of durable interlocking concrete blocks, which prevent soil erosion and runoff. These walls are visually appealing and require low maintenance, making them a practical choice for landscaping and property management. Stonebloc walls provide a reliable and eco-friendly solution for a variety of land management needs.
For retaining walls the help divide the land and reduce environmental impact, reach out to us:
https://www.envirocon.co.nz/pages/contact-us
Stonebloc retaining walls combine strength and timeless design. To ensure that your wall is looking its best throughout its life, make sure you’re maintaining it. Stonebloc is made to be low maintenance, so it won’t take you much time.
What happens when you don’t keep up with maintenance
If you don’t complete regular maintenance, there could be a number of things that could occur. These are all avoidable if Stonebloc is designed as it should be and regular maintenance is conducted.
- Moss and other buildups on the facia of the wall
- Water leakage
- Graffiti
Here are some examples:
For the easiest maintenance, it starts with the design & installation
Design
Stonebloc is made to be a low-maintenance retaining wall, but there are ways to reduce the time and effort you need to put in. Often, this comes at the design stage of your project - before a single block has been placed.
A waterproof barrier (like a mudguard) can be engineered into the design. Adding this will ensure that unsightly leakage between the blocks is prevented. If you’re considering this for your Stonebloc retaining wall, make sure to take a thicker wall design into consideration at the calculation stage.
Along with a waterproof barrier, it is vital to have good draining with your retaining wall. For Stonebloc designs, we’d recommend a drainage system that allows for a high crush resistance that can be used vertically or horizontally.
Here’s what to consider for retaining wall drainage:
- Getting the right backfill and drain coil for your project is vital. This ensures water/moisture can be effectively drained
- Take into account the type of soil or clay - this may affect the overall design and the maintenance approach after
- Surface water needs to be taken into account. If there are gutter downspits nearby that drain near your wall, divert it away (DIY Retaining Wall)
On its own, Stonebloc is strong with a minimum 20MPa. If you’re needing something stronger, however, you can custom order Stonebloc with a range of specialist blends. This strengthening is done at the production stage when the wet concrete is poured into the Stonebloc mould. The agents that we add to these specialist blocks will help with added durability.
Installation
When installing, use this time to ensure all blocks are aligned correctly. Getting this correct the first time around, means future maintenance is easier.
To get your Stonebloc installation right, watch this video with James:
With installation, you need to ensure you’ve brushed all the blocks of debris. By not brushing away debris, stacked blocks will not sit flush on top of each other. Not only does this cause issues in installation, it also will cause maintenance issues to arise. Chipping of the blocks can occur if installation is not correctly done, and water/moisture drainage can be affected.
One thing you may encounter during installation is block gaps on alternative layers. Stonebloc is not made to be mm precise so they’re quite forgiving during installation. This can be remedied quickly at installation with shims, however, in most cases, these gaps will level out over time. This can still be corrected once the wall is installed, but it can take longer, costing you more money and time as you need to deconstruct the wall.
To help create accurate retaining walls fast, you can use one of our Stonebloc Installation Templates. Getting the base layer of a Stonebloc retaining wall correctly aligned is vital; getting it misaligned will not only make the remaining layers’ installation difficult, it will also lead to inaccuracy. This inaccuracy leads to retaining walls that are harder to maintain over the walls lifetime.
The templates are available in two size
- Single
- Double
Tips for keeping your Stonebloc retaining wall in good condition
ADD GRAFFITI PROTECTION
For walls that are facing the public, it may be worthwhile to consider an anti-graffiti coating. Without adding a coating, graffiti removal from an unprotecting retaining wall can be costly and cause damage to Stonebloc’s facia. This needs to be applied annually
Some of the benefits of using protective coating include:
- Remove graffiti is easily
- No ghosting or shadowing is leftover
- You eliminate the need to hire a professional graffiti removal service as you can do it yourself
- A lot of graffiti protection coatings are also high weather resistance. In many instances, this will protect your Stonebloc wall from UV and salt spray
- The effects of direct and pollution can also be reduced, allowing it to keep it looking the same as when it was first installed
ADD A MOSS GROWTH PREVENTION COATING
If moss occurs, growths can be controlled with a 1: dilution of bleach/water. Just apply over the affected area using a watering can and leave for 2-3 minutes then wash off with a hose and brush. Make sure you use a lot of water to dilute the residue as the bleach will not only kill the moss & algae but other plants as well. It may also change the colour of the block walls. To fully control the spread, you may need to add 2 or 3 applications.
If weeds do appear between the joints of blocks in your Stonebloc wall, they can typically be removed by hand, hot water, steam water blaster, or controlled with weed killer. When using weed killer, make sure it's suitable for retaining walls specifically as it’ll be less likely to stain or discolour the blocks. Always follow the manufacturer’s directions on use and application.
WATER BLAST REGULARLY
Waterblasting is the most effective way to keep Stonebloc clean.
We do not recommend high pressure water blasters as this can damage Stonebloc’s facia, causing an unsightly finish of the wall.
HIDING THE LIFTING PINS
Over time, you may want to hide the lifting pins that sit on top of Stonebloc. This will give you a smooth, polished look. Depending on your project, you could use a cementitious leveling mortar to create an even finish.
Here are the features of a mortar that we’d recommend:
- The ability to apply with thin layers, for easy workability
- Be able to work on materials such as concrete, mortar, and masonry
- Strong, both mechanically and with substrate adhesion
- Good resistance to water & moisture
For any questions about maintaining your Stonebloc wall, reach out to us.
We are excited to announce that we have developed a new program to recognize and reward contractors who have demonstrated exceptional skill and expertise in the installation of our Stonebloc range. Our program has four levels: Bronze, Silver, Gold, and Platinum.
As a contractor, becoming a Stonebloc Accredited Contractor is a great way to differentiate yourself from other contractors in the industry. By completing the training and meeting the required criteria, you will be demonstrating to your clients that you are fully qualified to install Stonebloc to the highest standards. Additionally, by having a proven track record of delivering outstanding results, you will be showing your clients that you are committed to providing the best possible service.
(Dan, Tex, and Louesito from Ground and Pound with their certificates after completing their Stonebloc Accredited Contractor's training)
But the benefits don't stop there, as an Accredited Contractor, you will also benefit from a range of exclusive perks and support, such as:
- Discount on the wholesale price of our products
- Easy-to-use design software
- Personalized service and support from a dedicated support person
- Free technical support
- Installation plans and detailed instructions
![]() | ![]() |
![]() | ![]() |
It's important to note that Stonebloc isn't the best fit for every retaining wall contractor. We also have ambitious growth plans so we want to partner with contractors that share our ambition. Below is a list of what we're looking for in a Stonebloc Contractor:
- A commitment to delivering exceptional customer service
- A proven track record of delivering high-quality retaining walls
- A desire to continuously improve and stay up-to-date with the latest industry trends and techniques
- A willingness to collaborate and work closely with our team
- A desire to grow your business and take advantage of the opportunities that our Accredited Contractors program provides
If you are interested in becoming a Stonebloc Accredited Contractor, please visit contact us for more information on the requirements.
We look forward to working with you and helping you to grow your business.
Stonebloc retaining walls are a versatile and durable landscaping solution that can enhance the aesthetic appeal of any property while also providing functional benefits. They are particularly popular in New Zealand due to their natural-looking finish and ability to withstand the elements. Not only do they improve the overall appearance of a property, but they also increase its value.
When it comes to housing in New Zealand, there are a few different types to consider. Terrace housing, for example, is a type of housing where a row of houses is built closely together, sharing one or more walls. These houses are typically smaller in size and are a popular option for urban areas where space is limited. Stand-alone houses, on the other hand, are individual houses that are not attached to any other property. These houses are typically larger in size and are popular in suburban and rural areas. Multi-unit housing refers to buildings that contain multiple dwelling units, usually apartments. These are usually popular for high-density housing.
Standalone House | ![]() |
Terrace House | ![]() |
Multi-Unit House | ![]() |
Regardless of the type of housing, Stonebloc retaining walls are an ideal solution for creating functional outdoor spaces. For terrace houses, they can be used to create a sense of privacy and separation between properties while also providing functional benefits such as retaining soil or creating level terraces. For stand-alone houses, they can be used to create raised garden beds, level out uneven areas and enhance the aesthetic appeal of the property. Multi-unit housing buildings can also benefit from Stonebloc retaining walls, they can be used to create more outdoor spaces for the residents, and also can be used as a sound barrier.
(The Standard Stonebloc Block)
One of the best things about Stonebloc retaining walls is that they are easy to install, no matter the type of housing. Whether you have a terrace, stand-alone or multi-unit house, a Stonebloc wall can be installed quickly and efficiently. The standard size of the blocks is 800 x 400 x 400mm and they weigh 300kgs, making them easy to handle and maneuver during the installation process. The minimal foundations required for installing the wall makes it easy to set up and it can be done with minimal disruption to the surrounding area.
(Installing with Stonebloc)
Many existing homeowners often switch to Stonebloc retaining walls as they have experienced issues with their timber retaining walls. Timber retaining walls are prone to rotting, warping and insect infestation, which can cause them to fail over time. Stonebloc retaining walls, on the other hand, are made of concrete and are not susceptible to these issues. They are also more durable and can withstand the elements better, making them a more reliable option for retaining walls.
(Stonebloc retaining wall on the left, timber retaining wall on the right)
Installing a Stonebloc retaining wall not only improves the aesthetics of the property but also adds value to it. The functional outdoor spaces created by the wall can be used for entertaining, relaxing, and even for additional housing. It increases the overall appeal of the property and makes it more attractive to potential buyers. By adding a Stonebloc retaining wall, homeowners can increase the value of their property, making it more desirable and potentially increasing the sale price. Additionally, the durability and longevity of Stonebloc retaining walls make them a smart investment for homeowners looking to improve their property and add value over time.
In conclusion, Stonebloc retaining walls are a great addition to any property in New Zealand, regardless of the type of housing. They are easy to install, durable, versatile, and customizable. With the ability to transform a house's outdoor space and add value to the property, it's no wonder that they are a popular choice among homeowners. If you're looking to enhance your property and create functional outdoor spaces, consider installing a Stonebloc retaining wall with the help of a Stonebloc Accredited Contractor.
As a homeowner, building a retaining wall can be an intimidating endeavour if you don’t know where to start. It’s important to seek simple, cost-effective solutions while being able to bypass the construction industry jargon. Understanding the overall process, from quoting, to installation, and maintenance, can help ease any confusion and ensure a successful outcome.
We have put together a guide for homeowners who are investigating solutions for retaining walls. If you are needing a standard or conventional retaining wall, this guide will serve as an easy-to-follow checklist to get you started and prepared.
Remember, the homeowner assumes responsibility to check this list and ensure their designed retaining wall meets the requirements and regulations for installation.
Council Consent
While most types of walls do need consent from the council for safety, some do not. However, retaining wall requirements may vary between different councils. So, it’s important to check with your local council, and make a note of what you need.
Walls that are less than 1.5 metres high, and support nothing such as a garden, often don’t need consent. If you're in Auckland, use this tool to give you a rough idea of if you need consent or not.
(Auckland Council's Retaining Wall Tool)
Buildability
There are many external factors to a retaining wall to consider, therefore, construction of the wall needs to be realistic and designed thoughtfully.
For example, consider:
- Consider how trucks and other large machinery will access the site. Is the space large enough for them?
- Can the blocks get to the planned retaining wall location?
- Is there adequate drainage for rain and water?
- If you have a sloped property, consider how the slope, surrounding buildings, and structures might be affected in the event of storms, heavy rain, or even natural disasters such as earthquakes.
- Heavy rainfall or natural disasters can put pressure on retaining walls if they’re constructed on a slope. They are at risk of cracking, moving, or even collapsing, which is, of course, a safety concern. There are several factors that can put slopes at a higher risk. For example, if the surface material is soft or loose, comprises of mostly soil, has a gradient of over 35 degrees, or if the slope has been cut into. Take the time to research signs and other risk factors for slopes before going ahead with a design.
- Make sure you consider any other restrictions to the site. Check for blockages such as trees. Also, make sure the ground you are planning to build upon is solid and not soft.
- Retaining walls are a structure and therefore, need to be designed with expert engineering. Getting the help of a contractor, such as a Stonebloc Accredited Contractor, will help avoid any headaches. Stonebloc Accredited Contractors are professionals who will understand how your project will work best with Stonebloc.
Tip: Take some photos of where you want your retaining wall to be constructed. Send them to your Envirocon representative who will help determine what you need.
Engineering Consent
Specific engineering is used mostly for consent purposes. Be sure to consider the following:
- If you need council consent, you do need a site-specific design.
- If your site conditions lay within a number of Stonebloc ready-made designs, you will only require an engineer’s short review.
- Allow time to issue design calculations for a PS1 document, which is a producer statement used for specialist work such as engineering. A producer statement such as a PS1 helps the council determine whether the building work meets the Building Code regulations.
- Geotech report and pass it on to a consultancy for the design and consent process. Geotechnical engineers are important as they help calculate factors that will influence how the retaining wall will be designed and built, such as considering how much weight the site and wall itself can hold.
While designing and building a retaining wall for your home can seem daunting, it doesn’t have to be. Nor does it have to break the bank. This checklist should breakdown the tasks you need to do and provide a place for even newbies to begin. Following this checklist will reduce delays, unnecessary costs, and ensure your retaining wall is safe, durable, and aesthetically pleasing.
Steve and Sopa are a Pokeno based couple who recently chose to work with Stonebloc to build their retaining wall. They wanted to create a retaining wall where their fruit trees could grow above, while doubling as an entertainment area for their home. The couple were meticulous and heavily researched the design and buildability of their retaining wall plan. This helped ensure a successful construction of their retaining wall and will make sure it stands the test of time.
(Steve & Sopa's Stonebloc retaining wall, with their fruit trees sitting on top)
After reviewing the checklist, we’d recommend reaching out to our Stonebloc representative to see how Stonebloc would work for you and your home.
Stonebloc is a high-productivity, durable precast concrete retaining wall system. At the heart of the system is the 800 standard block which weighs 300kg and is used to build the majority of a Stonebloc retaining wall. However, there are a series of very important, less commonly used Stonebloc blocks which can enhance your wall.
In this article, we provide an overview of these blocks and the vital role they play in delivering a comprehensive, high-aesthetic retaining wall system.
Base Blocks
Base blocks add mass to a wall and are crucial for higher gravity walls to resist overturning and sliding forces. Stonebloc walls are designed based on the first engineering principles for conventional gravity-based systems.
With Stonebloc base bocks, walls do not require embedment and have minimal foundation requirements.
Variations include:
- 1200 Base Block (typically used in walls 1.8m high and above or when a source of the permanent load is applied on top of the wall)
- 800 Base Block (typically used in walls 1m high and above)
The base blocks (as well as the rest of the Stonebloc range) were used extensively through the Ara Hills Development in Orewa.
Cappers
Cappers deliver a clean finish to the top of the wall and also allow walls to be built in increments of 200mm. They also provide a flat surface for top-mounted fencing or balustrades.
Variations include:
- 200 Capper
- Half Capper
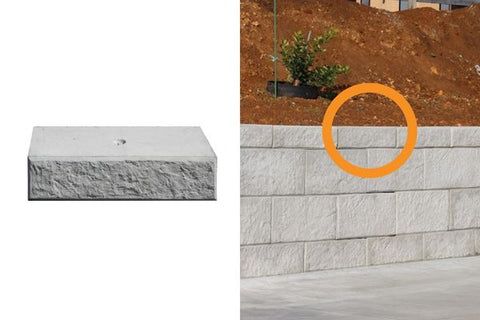
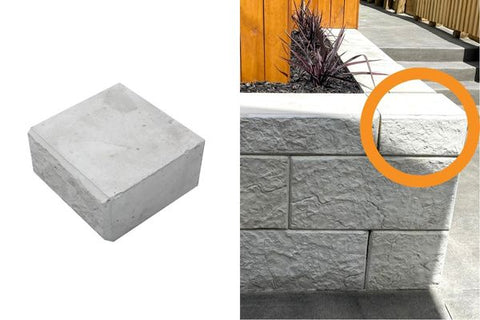
The Bomb Point Drive development from Jalcon Homes used a mixture of cappers to create a smooth top layer to install balustrades.
Flat Top Double Ended Block
Sitting at the top of a retaining wall, this block continues the texture around corners. By using the double ended block, a seamless finish is created. It also allows for a flat surface for fencing/balustrades.
Variations of the block include:
- 800 Left Hand
- 800 Right Hand
- 400
Standard Double Ended Block
This block continues the texture around corners. By using the double ended block, a seamless finish is created.
Variations of the block include:
- 800 Left Hand
- 800 Right Hand
- 400
200 Capper Double Ended Block
Instead of using the 800 flat top, a capper can be used on the top layer for a more refined design. Adding a capper to your builds means a flat surface for fencing/balustrades.
Variations of the block include:
- Left Hand
- Right Hand
To start building with Stonebloc Specialist blocks, get in touch with us today.
Imagine a retaining wall made specifically for New Zealand's unique environment. Stonebloc is one of the few retaining wall systems in New Zealand that fully utilises locally sourced and manufactured materials.
Stonebloc is a gravity retaining wall system with an interlocking solid concrete block at its core. It's designed around the concept of timeless retaining - fast installation with minimal labour input, future-proofed aesthetics, and comprehensive engineering. These features have been created with New Zealanders and the way they work at the forefront.
The concrete block that is central to the Stonebloc system
The main material used for Stonebloc, concrete, is all sourced in New Zealand. With the continuous and growing issue with supply chains globally, Stonebloc is able to avoid issues with material supply. The supply of concrete has not been as affected, so Stonebloc has dependable lead times and pricing.
Its timeless look means it can fit in both city and rural areas, blending seamlessly into its surroundings as time goes by. The split stone facia replicates much of the natural environment that can be seen across various parts of the New Zealand landscape.
Not only has Stonebloc’s look been centered around New Zealand, but so has its engineering. Unlike most other retaining systems on the market, it is purpose-built for this country. A great example of this is the suitability of Stonebloc gravity walls with Auckland’s volcanic rock where earthworks have to be minimized and piling is impossible. With Stonebloc, simply stack the blocks, backfill and the wall is complete.
The benefits of Stonebloc aren’t just limited to the product itself- Stonebloc is a product at the Envirocon Product Stewardship Scheme, NZ’s only construction-related product stewardship scheme. The Scheme takes a circular economy approach to product design - our blocks can be non-destructively dismantled at end of life and repurposed.
Stonebloc is the retaining wall solution made by kiwis, for kiwis.
Stonebloc is a modular gravity based retaining wall system and is often used as a substitute for the more traditional Gabion basket system - another gravity based wall system. In this blog we’ll provide an overview of Gabion baskets and how it differs from Stonebloc.
About Gabion Walls
The word “Gabion'' has Italian origins, meaning big cage. Gabion Walls serve either a decorative or functional purpose. They feature a large metal cage filled with rock and stone (Ilker, 2016). Like all modular gravity wall systems, they are very flexible and are able to withstand movements from undercutting or land slippage.
Gabion walls tend to be used on road reserve areas at the subdivision level of development, or for supporting heavier civil infrastructure. One of the perceived benefits of Gabion baskets is the on site fabrication and placement of stones. In contrast to this, a limitation of Gabion is its inability to accommodate land deformation or provide landslide remediation.
About Stonebloc
Stonebloc is a gravity retaining wall system. At the heart of the system is a solid concrete retaining wall block with a unique interlocking design which provides a shear key in both horizontal directions. This means Stonebloc retaining blocks lock together with ease.
Stonebloc is designed around the concept of timeless retaining - fast installation with minimal labour input, future proofed aesthetics, and comprehensive engineering.
Stonebloc was designed to fill a gap in the New Zealand retaining wall market by combining these benefits into a single product and construction system.
The result is a system that delivers the speed and durability of precast concrete at a timber price point.
Stonebloc and Gabion Quick Comparison Table
Attribute | Stonebloc | Gabion |
Foundation | Compacted gravel foundation | Compacted gravel foundation |
Installation Process | Stack blocks like LEGO® | Construct cages onsite and fill with stones |
Backfill | Free slowing drainage material and drainage coil | Free slowing drainage material and drainage coil |
Resilience | Solid concrete blocks with 100yr design life | Galvanized steel cages |
End of life | Non-destructive dismantle and reuse | Recycling aggregate |
Structural capability | 400-800mm thick Gravity walls with option to reinforce with geogrid to create MSE wall | 1m-3m thick gravity walls |
Conclusion
While Stonebloc is not the only gravity wall system available on the market, we argue its unique combination of features and benefits ensure it is the best option. While Gabion traditionally has fulfilled an important role in retaining, its lack of resilience handicaps it in a world increasingly focused on smart resource use.
We’ve launched a Stonebloc Contractor's Training Programme, and on the 20th of April, we had our first session. In that week, Solid Landscape Solutions Ltd, RVT Construction, RF Masonry, and First Civil all learned how to build a 11.2m long, 1.4m high Stonebloc retaining wall.
In these sessions, we demonstrate to contractors how Stonebloc is the fast-to-install, cost-effective retaining wall solution.
Why we’re offering training
Stonebloc is experiencing rapid growth in demand and we need external contractors to install retaining walls. In partnering with experienced contractors, we’re able to focus on manufacturing high quality blocks and developing robust innovative engineering, while contractors do what they do best - install great looking walls, fast.
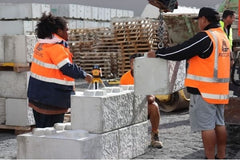
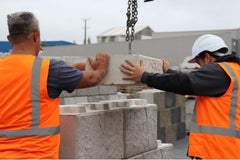
During a training session we cover:
- Key uses and the markets targeted
- Block types, weights, and dimensions
- Preparing the site (Running a string line, levelling fines, etc)
- Placing the first block & second base blocks
- Using the Stonebloc Template
- Placing more blocks / second and third layers
- Stacking the blocks
- Dismantling the wall
These training sessions are held at our contractors training area located in our Penrose, Auckland factory. For those who need to brush up on their Stonebloc knowledge, there is also an online course you can do.
To give you a better idea of the Stonebloc system, listen to James tell you about Stonebloc’s installation.
What Contractors Think of the Training Programme
"The training session the RVT team had was really insightful into the development and work that has gone into the Stonebloc product, so much easier and aesthetically pleasing than a timber wall. I would definitely recommend this system over a traditional timber retaining wall . They are far more durable and no need to paint or cover with plants as it looks really smart."
- Robbie Van Tiel
Solid Landscape Solutions
“We really enjoyed working with the blocks and look forward to starting new projects”
- Peter Rogers
“The Stonebloc system is good, the blocks are nice to work with and the end product looks goood. Our boys enjoyed it and are looking forward to working with them again.”
- Rhys Faleafa
How to get involved
If you’re interested in becoming a Stonebloc Contractor, get in touch today. We’ll work alongside you to make sure you get projects you’re interested in.
Stonebloc is a precast concrete gravity wall system launched in 2015. Stonebloc was designed to fulfil an unmet demand in the retaining market - fast, flexible, strong, and great looking retaining. This is in contrast to masonry retaining walls. Masonry has been around for thousands of years, and although it has its benefits, it also has its downsides. In this blog we run through the major differences between the systems.
What is a Masonry Retaining Wall
Commonly referred to as cinder block walls or block walls, concrete masonry is a well-known, well-used material in construction. Structures are made with a combination of masonry blocks and mortar.
In typical circumstances, these retaining walls have the following features:
- A concrete footing
- Hollow-core blocks (Approximately 410mm long and 200mm wide)
- Mortar
- Rebar (For vertical reinforcement, if required)
What is a Stonebloc Retaining Wall
Stonebloc is a gravity retaining wall system. At the heart of the system is a solid concrete retaining wall block with a unique interlocking design that provides a shear key in both horizontal directions. This means Stonebloc retaining blocks lock together with ease and stay together.
One of the most common structures for Stonebloc gravity retaining wall has a mixture of block types. These blocks are a 1200 base, an 800 base, 800 standard block(s), and a 200 Capper block.
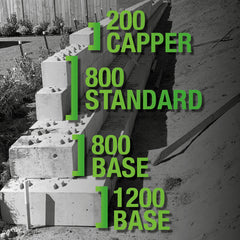
Stonebloc is designed around the concept of timeless retaining - fast installation with minimal labour input, future-proofed aesthetics, and comprehensive engineering. The result is a system that delivers the speed and durability of precast concrete at a timber price point.
Features of a Masonry Retaining Wall vs Stonebloc Retaining Wall
The most noticeable difference between Stonebloc retaining walls and block retaining walls can be seen at installation. Stonebloc uses interlocking shear keys to form its gravity wall solution. Masonry requires more materials to be deemed “sound” - this includes mortar and rebar.
The other larger point of difference is aesthetics. In most cases of masonry walls, the blocks have a smooth, plain facia. Stonebloc on the other hand has a textured facia, designed to imitate the natural surroundings its in.
Stonebloc | Masonry | |
Segmental System | ???? | ???? |
Interlocking Blocks | ???? | |
Facia Variation | ???? | |
Engineered | ???? | ???? |
Mortar Bed | ???? |
Benefits of a Masonry Retaining Wall vs Stonebloc Retaining Wall
Stonebloc has been designed with engineers, designers, and installers in mind. It’s build ready designs and minimal foundations mean you can create retaining walls fast. Masonry retaining walls are used for this same audience but require more time due to mortar being the connective material between blocks.
Once walls are completed, Stonebloc also comes out on top. Both systems have a timeless look, reassuring your retaining walls will blend into the environment as time goes by. However, Stonebloc has the benefit of being able to be non-destructibility dismantled. What this means is that if you need to access utilities, you remove the blocks that are closest. With masonry walls, there is more work. You’d need to demolish the entire wall to get access, costing you extra in demolition and then effectively paying twice for the same wall.
Stonebloc | Masonry | |
Build Ready Designs | ???? | |
Minimal Foundation | ???? | ???? |
Fast Installation | ???? | |
Non-Destructive Dismantling | ???? | |
Timeless Look | ???? | ???? |
Stonebloc uses minimum extras in their gravity wall. It’s the pure strength of the concrete blocks that are keeping structures upright. Whereas masonry walls you need to take into account the mortar. Not only is this an added cost to you, but it’s also another box to check off when installing with masonry blocks.
Where to use a Masonry Wall
Masonry walls have there place as a traditional building solutions. In a general sense, they are great for retaining walls. They offer stability through their rebar systems and mortar beds.
The areas that provide strength to the system, also prove to be weaknesses of the system. They do not allow for flexibility of the system. Although touted as low-maintence, if you do need to replace part of the wall it is far more complicated compared to a solution like Stonebloc.
Where to use a Stonebloc Wall
A flexible and modular solution is created with the Stonebloc system. For a simple gravity wall, our generic designs can reach 2.4m with 0, 5, and 12 kPas. Outside of these generic designs, Stonebloc’s engineering can help produce almost any outcome.
In the event that you’re needing more structural, engineered support for your Stonebloc walls, we’ve recently launched MSE walls.
Stonebloc is the flexible solution. Get in touch with us today to get timeless retaining.