Engineering Basics
Before we dive into what a gravity wall is and how it could work for you, you'll need to understand a couple of engineering basics.
Stonebloc is primarily a gravity- based retaining wall system. A gravity wall system relies on the combined weight of the blocks to resist overturning forces.
Every wall with a load pushing against it supports a “wedge” shaped load. The wedge is defined as the area which extends beyond the failure plane of the material type present at the wall site and can be calculated once the friction angle is known.
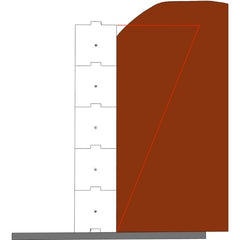
All walls need to withstand four key forces:
![]() | Sliding Ability of the retaining wall structure to overcome the horizontal force applied to the wall. |
![]() | Overturning Ability of the wall structure to overcome the overturning moment created by the rotational forces applied to the wall. |
![]() | Bearing Capacity Ability of the underlying soil/foundation to support the weight of the wall structure. |
![]() | Global Stability Ability of the internal strength of the material to support the complete material mass. |
How the Stonebloc Gravity Wall Works
Stonebloc gravity retaining walls work with a combination of interlocking shear keys and the weight of concrete.
The shear keys that are located at the top of Stonebloc blocks work to resist sliding and lateral soil pressure. The shear key does not reduce the impact of overturning. This is rectified by the weight of the blocks themselves - the rotation point at the bottom of the block helps to push the block back to its original position.
Relying on gravity and shear keying in two horizontal planes it achieves its strength as either a standalone gravity wall or a retaining wall able to withstand high surcharge levels.
One of the most common structures for our Stonebloc gravity retaining wall has a mixture of block types. These blocks are a 1200 base, an 800 base, 800 standard block(s), and a 200 Capper block.
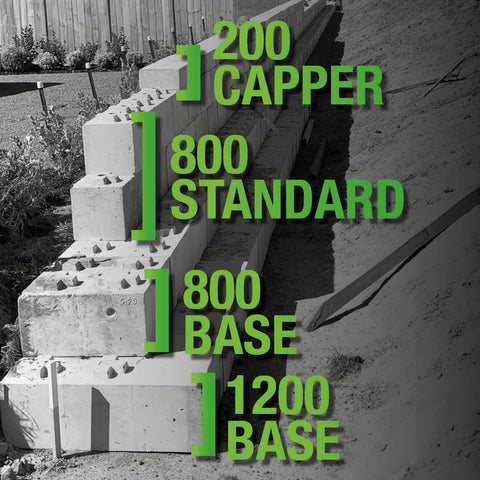
(Annotated picture of a Stonebloc wall in situ pointing out the different block types)
The benefits of Stonebloc’s gravity wall
By choosing Stonebloc, you'll get access to a unique combination of benefits. Some of these include:
- Easy to install
- Fast installation
- Can reach a height of 2.4m
- Various kPa’s: 0 kPa, 5kPa, 12kPa
- Resists sliding and overturning
- Can be adapted to suit many projects and situations
Common instances of a gravity wall
Stonebloc’s retaining walls are most often seen in residential developments. The flexibility of the system, however, does mean that you are limited to one
Here are some Stonebloc case studies:
- A contractor’s experience using Stonebloc
- A High Density Housing Developer
- A Greenfield Housing Developer
You can also use Stonebloc gravity walls for low landscaping walls and slope rehabilitation.
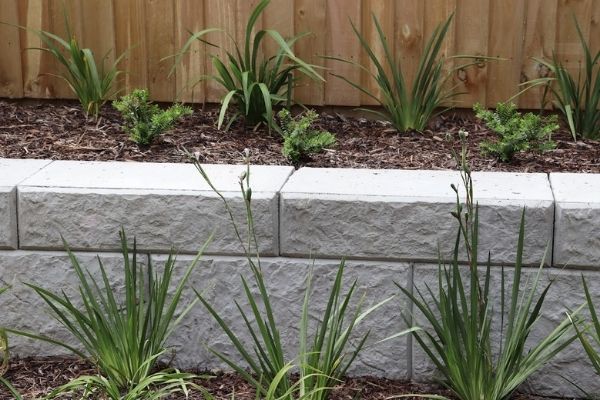
(Stonebloc's Low Landscape Wall)
If you’re wanting retaining walls that can withstand heavier loads, you may be interested in Stonebloc’s Reinforced Earth Walls.
Build your own Stonebloc Gravity Wall today!
Stonebloc is excited to announce the addition of a mechanically stabilized earth (MSE) reinforcing option. This innovation in design capability for Stonebloc walls allow you to build higher, and sustain greater loads. In fact our customers' first lot of Stonebloc MSE walls are 5m high with a 24 kPa surcharge!
What is an MSE Wall?
A Mechanically Stabilised Earth (MSE) retaining wall is a composite structure consisting of alternating layers of compacted backfill and soil reinforcement elements, fixed to a wall facing. The stability of the wall system comes from the interaction between the backfill and soil refinements, involving friction and tension. The wall facing is relatively thin, with the primary purpose of preventing erosion of the structural backfill. This results in a structure that is flexible with the ability to carry a variety of heavy loads. It is also a fairly orthodox design approach, often used for large public infrastructure projects.
MSE walls tie the Stonebloc wall elements (the individual blocks), to the retained soil using synthetic geogrid. In the case of Stonebloc, this will be most used for tall retaining walls (Above 2m and above 12kPa).
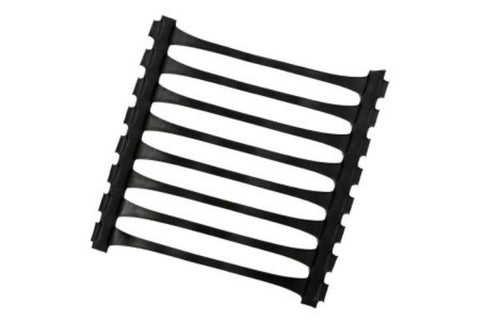
MSE is a cost-effective, and stronger solution when building retaining walls with large loadings. There are numerous different MSE systems out on the market, however only Stonebloc MSE walls combine speed of installation (including eliminating the need for bracing the face panels), with customisable aesthetics.
Benefits of an MSE Wall:
- Bearing pressure is distributed over a wide foundation area
- Extreme wall heights can be achieved
- Extreme loads can be carrier (bridge abutment footings, cars)
- High resistance to earthquakes and other dynamic forces
- Free-draining, due to granular backfill and open panel joints
- Very versatile. Special design can allow for nearly any configuration
- Rapid, predictable, and repetitive construction
- Superior finished wall alignment
How Stonebloc’s MSE Wall Works
Synthetic geogrid is embedded into Stonebloc blocks at the production stage. Usually, the geogrid is cast in the block during manufacturing with an exposed tail.
When building, the exposed geogrid is tied to more geogrid, which sits separately from the wall. The backfill and soil is compacted as the wall is built.
Interested in building a Stonebloc MSE wall? Get in touch with us!
Townhouses, flats, and units have grown in popularity in recent years - up to 40% according to Stats NZ. With this growth in demand for infill housing, space is a premium: you want to be making the most of every square inch you have. The product that can help maximize your land is Stonebloc.
The Stats/ Trends
The upwards trend of new townhouses
With New Zealand’s current property boom, more houses are in demand. Traditionally, the classic Kiwi home has been a standalone house on a relatively large plot of land. This has changed over the years, however. To get more houses into various cities, there has been a sharp increase in high-density housing.
According to Stats NZ, in the year ended September 2021, 46% of all new homes consented nationally were multi-unit homes (townhouses, apartments, and flats}. Adding to this, in Auckland alone two-thirds of the builds consented in the last year were for multi-unit homes.
(StatsNZ, 2021)
To give you an idea of the growth going with high-density housing, here is a comparison of new homes consented between 2011 and 2021.
The future of homes in New Zealand
Auckland is likely to continue in an upwards momentum, building new multi-unit dwellings, according to Kainga Ora. As part of a solution to the housing crisis, high-density houses are made by redeveloping underutilised land. This creates homes for multiple families, alleviating some of the stress made by the crisis. With the city often seen as a trendsetter to other New Zealand locations, this impact could spread across the country.
The shift to smaller houses means as an industry we need to adapt the way we work to new environments. Methods and products that traditionally worked for a standalone house won’t necessarily work with high density housing. Luckily, there is a solution to help with this increase in demand - Stonebloc.
How Stonebloc is Made for Infill Housing
Stonebloc is a modular retaining wall system specifically designed to fit a variety of building designs. Ranging from large greenfield developments to high-density housing, the modularity of Stonebloc gives you options. With the flexibility that Stonebloc’s solution offers, retaining walls can be adapted to all types of high-density housing.
The system is made up of a series of concrete blocks. When you see them, you may reminisce as they’re similar to the beloved childhood toy LEGO. These blocks stack together in a running bond to form countless numerations of retaining wall designs. The full range has a selection of standard, flat top, capper, base, and double-ended blocks. By having these variations, your wall(s) can be made to suit your project no matter the size.
Building on the Boundary
The modularity of the Stonebloc system makes building throughout easy. Stonebloc is a gravity wall, meaning the combined mass of the blocks resist any overturning forces. Because of this, the walls can sit parallel to the boundary line. Better yet, this will not impede when you’re meeting council requirements.
Made for Disassembly/ Modular Build
To help dampen the negative effects of the housing crisis, housing needs to be built fast. Stonebloc is a modular retaining wall system, making installation quick and easy. It also means that disassembly is simpler than traditional retaining walls. Modularity comes with a long list of benefits. Some of these include:
- Made for disassembly. So if you need to access utilities or replace a single block you can. By going modular, you don’t need to replace the whole wall.
- Faster installation.
- Better quality assurance
- Environmentally Friendly
- Cost-effective
- Fully customizable
Stonebloc is the retaining wall solution for high-density housing. If you’re wanting to solve your retaining wall woes for your project, click the link below to get in touch with us.
https://www.envirocon.co.nz/pages/contact-us
Our Stonebloc is a high productivity gravity retaining wall system. At the core of the system is a concrete block featuring a unique shear key and facia. Combined the block and the engineered system deliver a more durable, better looking retaining wall at an impressively low cost that’s similar to timber.
Chances are, if you are reading this you already understand all the benefits Stonebloc offers over retaining wall systems. Here are our top nine tips for installing a Stonebloc retaining wall.
- A firm and level foundation and site set up is important. In good ground conditions all you need is a levelling layer of fines. Use a level to smooth out the base and then compact before placing the blocks. Consult your geotechnical engineer if you have any questions about the foundation requirements for your wall.
- Correct placement of blocks: The interlocking design of the blocks deliver a high productivity, high speed installation rate. However, getting the spacing correct on the base layer is essential for an accurate build going forward. Stonebloc offers a ‘install stencil’ which allows you to check block placement as you go. Remember to run a string line along the length of the wall and place the blocks about 10mm away from it to ensure a straight, plumb wall.
- Clean/sweep loose debris: You need to make sure the foundation’s surface is clean prior to laying the first course of blocks - use a small hand brush to do this. Then make sure the top of the previous layer is swept free of debris too before you add the next layer. A Stonebloc wall is designed as a gravity system, so there’s no need for glue or grout so long as the surface below your current row has been swept clean.
- Running bond pattern: This classic placement provides more strength across vertical planes because it eliminates the continuous vertical joints that occur in stack bond walls.
- Review block layout design: You'll be supplied with a 3D render of your structure. It's important to review these templates to ensure the right block is put in the correct position. Placing the wrong block in the wrong position will result in a shortage of some blocks and surplus of others.
- Repositioning/adjustment of blocks during install: Blocks can be repositioned during the installation process by using a pinch/crowbar to leverage the block around.
- Check as you go: While Envirocon has a comprehensive quality control process, with thousands of blocks being produced each month the odd bad block may slip through. Check each block visually before placement to ensure there are no issues.
- Build the entire wall as you go: For optimal construction speed, building all levels of the entire wall as you move along the length of the wall allows you to easily identify incorrect spacing issues. Allow for block creep of about 2-3mm each block. Over longer wall distances this should be allowed for in the design of the foundation.
- Ready for backfilling pre-inspection: Backfilling retaining walls can be critical for optimal performance over the lifetime of the wall. Make sure all necessary geofabrics and any other specific engineering requirements are either in place or allowed for prior to any inspections.
Remember that no grouting makes Stonebloc easy to break down and install elsewhere if necessary.
Envirocon’s annual price check against common retaining wall methods has just delivered yet another great reason to make the transition to Stonebloc retaining. Stonebloc is now, on average, 10% cheaper than timber retaining according to independent cost comparisons undertaken by QV Costbuilder, a division of Quotable Value. This is the second annual independent price check commissioned by Envirocon to dispel the common misconception that great-looking walls have to cost more. Three core trends contributed to the result:
- Timber and associated material costs have increased an average of 20% driven by constrained supply and unprecedented demand. These factors have also led to significant blow-outs in lead times. (QV Costbuilder, 2021)
- Skilled labour shortages and regulatory changes have led to an average 12.5% increase in labour costs. (QV Costbuilder, 2021)
- Stonebloc’s continual investment in research and development through independent testing undertaken by the University of Auckland’s Engineering School led to a reduction in foundation requirements, reducing material costs.
Stonebloc is increasingly proving to be an antidote to the labour and material shortages plaguing the retaining wall market;
- Stonebloc is more productive and requires less skill to install. Our system requires minimal foundation preparation*, the blocks incorporate a quick-grip klaw for speed of movement, positively interlock with ease, and require only two semi-skilled labour units to install.
- Our scale, generic designs, and commitment to long-term customer relationships allow us to minimize cost inflation and meet delivery timelines.
- Our commitment to research and development delivers incremental productivity gains through all aspects of the retaining wall system.
There's never been a better time to make the transition to our Stonebloc retaining wall system.
Background Notes: QV Costbuilder is a division of Quotable Value and undertook the cost comparison in early June 2021 using the most up to date market rates. All costs were rounded to the nearest $5, and foundation costs included labour and material costs. Stonebloc provided wall profiles from our generic designs for a 5kpa wall with retail pricing. Freight was excluded from the costings exercise. Both timber and stonebloc costs exclude backfilling behind walls. *A levelling layer of fines is all that is required in good ground conditions.
Retaining contractors traditionally use timber to build the majority of retaining walls. Timber was a cheap and easy to source construction material. Generic designs made specifying and building a timber wall easy. However, for all the convenience of using timber for retaining walls, there are more than a few downsides.
It is a slow system to install and it is labour intensive. It doesn’t look great, and it degrades over time. More recently timber prices have increased while availability has decreased. This has a real impact on contractors' business - without timber you can‘t build walls. If you can’t build walls, you can’t earn an income. Timber shortages and cost increases aren’t expected to let up in the near future either.
Traditional timber alternatives, such as Keystone and Allan block, aren’t really viable alternatives as the finished installed price is as much as 50% more than timber.
Our solution? Stonebloc.
Stonebloc is a gravity, precast concrete block retaining wall system with a unique split stone finish. From the beginning, Stonebloc was designed to be the true timber alternative. While the block costs may be higher than timber, the speed and ease of installation mean the finished installed cost is the same. The result? Happier customers and more productive, profitable contractors.
How do we do this? Through great product design. We think about the people who will use our blocks, and the places our blocks will be used. Our design approach is guided by the power of simplicity because simple products are fast to learn and easy to use.
Think giant LEGO and you’ll start to appreciate how easy Stonebloc is to use. Installation means simply stacking the blocks on top of each other in a running bond pattern. Take that to the next level - given you’re simply stacking blocks, external delays are all but eliminated.
No more waiting for engineers or council to inspect pole holes or progress inspections of the build. Concrete trucks no longer need to be ordered. Simply stack the blocks, and backfill.
What about foundations? In good ground conditions, a simple layer of leveling fines (sand, builders mix etc) is required. Getting the base layer of blocks sitting level is also essential to delivering a good-looking wall, but we’ve designed an installation stencil to make this faster and easier.
Building the wall is only one-half of the equation. You still need to know what to build where, and how to price it. So we solved that problem as well. We teamed up with the engineering department at Auckland University to have the product independently tested. From that came a set of build and consent ready designs for 0 - 12kPa walls, 0 - 2m high. We also developed a chainage calculator which makes quantifying and ordering blocks easier.
You may be thinking at this stage it all sounds too good to be true. It isn’t, and that's why Stonebloc has been specified on some of Auckland’s largest residential developments. However, it does take a change of mindset. Stonebloc is about boosting profitability for contractors by doing more with less labour. The reward for this is stronger, better-looking, and longer-lasting walls. This results in happier customers. Most importantly it eliminates the current uncertainty of timber, positioning you and your business to take advantage of every opportunity.
Looking to diversify away from timber? Contact us today.
Stonebloc concrete blocks for beautiful retaining walls
Concrete blocks generally are a popular choice for the construction of retaining walls across New Zealand, with many designers preferring them to timber. Most people do prefer the durability and look of concrete retaining walls, but think that timber is more cost-effective - which it can be unless Stonebloc concrete blocks are specified.
Stonebloc delivers the benefits of concrete at a price point similar to timber’s (see “Stonebloc is cost-effective”). But there’s much more to the Stonebloc system than ‘just’ good prices.
Timeless – and time-saving - retaining walls
In tight spaces on developed sites, it’s especially important to do a great job in a short time – something the Stonebloc system delivers. With its aesthetic finish, you’re adding a uniquely classic look to your project.
Speed of construction is a big plus for projects operating within a confined area. Construction noise and disturbance can be an ongoing issue, and more and more companies appreciate the speed of construction that the Stonebloc retaining system offers.
Contractors can be in and out of a site much more quickly with the Stonebloc system, saving you time as well as money. Two people can build up to 120 metres of self-aligning wall in a day.
Each Stonebloc is 400mm thick solid concrete, using our unique design and interlocking shear key for an exceptionally robust wall on any site. The blocks stack easily and don’t need glues or grouts to hold them in place, meaning Stonebloc is delivering a standalone gravity wall in record time.
Vertical reinforcing can be included for cantilever walls, with tie-back options available for Mechanically Stabilised Earth (MSE) retaining walls. The Stonebloc system looks great too. For precast, residential, or architectural retaining walls up to 2.4 metres tall, the Stonebloc range is the perfect choice for your project. Our beautifully designed blocks enhance every landscaping selection, with a range of eight different shapes and sizes to ensure designs and finishes are suitable for every project.
The Stonebloc range includes standard blocks, base blocks, flat top blocks, and a 200mm-wide capper. Soil and moisture can’t leach through a Stonebloc retaining wall when combined with a correctly installed geomembrane lining, so excellent retaining performance over many years is a given.
If required, we’re happy to propose a design specifically for your project that ensures all appropriate codes are met. The Stonebloc system allows 90 degrees vertical retaining right on the boundary, freeing up more usable land for today’s small section sizes or tight access areas.
How Stonebloc works
When Stonebloc blocks are stacked next to and above each other, shear keys incorporated into each unit link together to offer shear strength in both horizontal directions and increase the structural integrity of your wall at each joint. The result is a high-performance solution with a high-quality finish that can be adapted to your requirements.
Geogrid tie-back and vertical reinforcing options are available, allowing the system to be used across a wide range of architectural applications. Whatever your design, the safety, and quality of the Stonebloc system are never compromised. Minimum strength (MPa) blocks are available to comply with engineering design specifications.
Stonebloc is cost-effective
The Stonebloc solid concrete block system, like its bigger Interbloc cousin, combines simple and rapid assembly with excellent shear strength, together delivering you a range of impressive benefits. Compared to other retaining wall systems, Stonebloc can offer cost savings of up to 32 percent. Third-party QS data suggests that Stonebloc is very price competitive against alternative solutions.
Sustainability in construction
Like all Envirocon blocks, Stoneblocs are made from excess wet concrete that would otherwise have gone to landfill. Strong modular design means walls can be easily unstacked and moved in the future if required. If you can’t reuse them elsewhere, they can be deconstructed and sold back to us under our unique BuyBack Guarantee. In addition to comprehensive warranties, this guarantee ensures true product stewardship.
Stonebloc is part of Envirocon’s product stewardship scheme, accredited by the Ministry for the Environment and the only construction-related one in New Zealand. With significantly less carbon embedded into Stonebloc from the start, your project can qualify for the appropriate Sustainability Accreditations, to meet the increasing regulatory requirements around sustainability in construction. This can include Greenstar (vertical construction); GreenRoads (NZTA); and ISCA (infrastructure projects). From design to commissioning, we provide unbeatable support throughout the whole process.